Plastic extrusion for durable and low-weight components
Plastic extrusion for durable and low-weight components
Blog Article
A Comprehensive Guide to the Refine and Advantages of Plastic Extrusion
In the large realm of production, plastic extrusion emerges as a highly efficient and essential procedure. Altering raw plastic into constant profiles, it deals with a variety of markets with its amazing versatility. This overview intends to clarify the elaborate actions associated with this technique, the types of plastic proper for extrusion, and the game-changing benefits it gives the industry. The taking place conversation promises to unravel the real-world impacts of this transformative process.
Understanding the Essentials of Plastic Extrusion
While it may show up complicated at initial glance, the procedure of plastic extrusion is basically basic. The process starts with the feeding of plastic product, in the kind of granules, pellets, or powders, into a warmed barrel. The designed plastic is after that cooled down, solidified, and reduced right into wanted lengths, completing the process.
The Technical Refine of Plastic Extrusion Explained
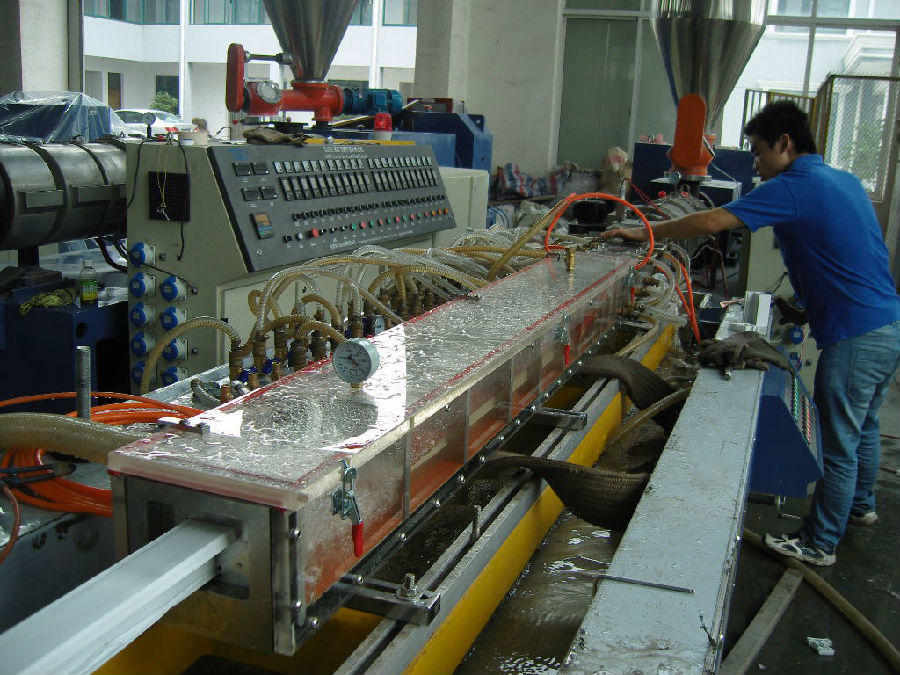
Kinds of Plastic Suitable for Extrusion
The choice of the ideal kind of plastic is an important aspect of the extrusion process. Various plastics provide one-of-a-kind buildings, making them more matched to certain applications. Understanding these plastic types can significantly improve the extrusion process.
Comparing Plastic Extrusion to Various Other Plastic Forming Approaches
Understanding the kinds of plastic suitable for extrusion paves the method for a broader discussion on just how plastic extrusion piles up against other plastic developing approaches. These include injection molding, blow molding, and thermoforming. Each technique has its special usages and benefits. Shot molding, as an example, is exceptional for producing detailed components, while strike molding is perfect for hollow items like containers. Thermoforming excels at developing shallow or huge components. Plastic extrusion is unrivaled when it comes to creating constant profiles, such as gaskets, seals, and pipes. It also enables a regular cross-section along the length of the item. Therefore, the option of approach mainly depends on the end-product requirements and requirements.
Trick Benefits of Plastic Extrusion in Manufacturing
In the realm of production, plastic extrusion provides several considerable advantages. One remarkable benefit is the cost-effectiveness of the procedure, that makes it an economically enticing production method. Furthermore, this technique gives superior product flexibility and improved manufacturing rate, thereby boosting total production efficiency.
Economical Manufacturing Approach
Plastic extrusion jumps to the center as a cost-efficient manufacturing approach in production. This process attracts attention for its capacity to create high volumes of product promptly and effectively, offering manufacturers with significant financial savings. The main cost benefit is the capability to use cheaper resources. Extrusion makes use of thermoplastic products, which are less pricey compared to metals or porcelains. Additionally, the extrusion process itself is reasonably basic, decreasing labor costs. In addition, plastic extrusion requires less energy than typical manufacturing approaches, adding to reduced operational expenses. The procedure likewise minimizes waste, as any type of malfunctioning or excess materials can be recycled and recycled, offering an additional layer of cost-effectiveness. Overall, the monetary advantages make plastic extrusion an extremely eye-catching alternative in the production industry.
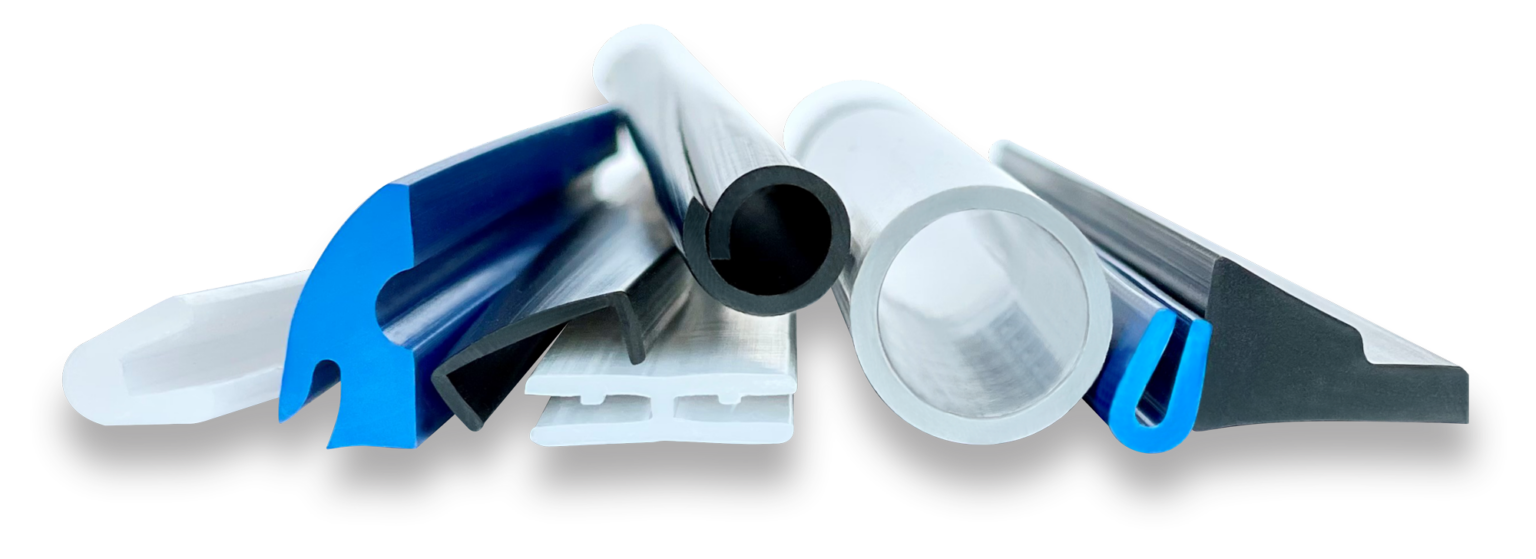
Superior Item Adaptability
Past the cost-effectiveness of plastic extrusion, another significant advantage click for more info in making lies in check my site its remarkable item adaptability. This makes plastic extrusion an excellent option for sectors that call for tailored plastic parts, such as auto, construction, and packaging. In essence, plastic extrusion's product flexibility fosters development while improving operational efficiency.
Enhanced Production Speed
A significant advantage of plastic extrusion depends on its boosted manufacturing speed. This manufacturing process enables high-volume production in a reasonably short time span. It can producing long, continuous plastic profiles, which substantially decreases the manufacturing time. This high-speed manufacturing is particularly advantageous in markets where big quantities of plastic components are needed within limited due dates. Few various other manufacturing processes can match the rate of plastic extrusion. Furthermore, the ability to maintain regular high-speed production without sacrificing item top quality sets plastic extrusion apart from various other techniques. The improved manufacturing speed, for that reason, not only makes it possible for producers to fulfill high-demand orders yet likewise adds to raised effectiveness and cost-effectiveness. This beneficial attribute of plastic extrusion has made it a favored choice in numerous markets.
Real-world Applications and Impacts of Plastic Extrusion
In the world of production, the method of plastic extrusion holds extensive relevance. The financial advantage of plastic extrusion, largely its cost-efficient and high-volume output, has actually changed manufacturing. The market is constantly making every effort for technologies in naturally degradable and recyclable materials, suggesting a future where the advantages of plastic extrusion can be maintained without compromising ecological sustainability.
Verdict
Finally, plastic extrusion is a reliable and highly effective method of changing basic go materials into varied products. It supplies numerous advantages over various other plastic developing approaches, including cost-effectiveness, high outcome, minimal waste, and style adaptability. Its influence is exceptionally really felt in numerous industries such as building and construction, vehicle, and customer goods, making it an essential procedure in today's production landscape.
Delving deeper right into the technical process of plastic extrusion, it begins with the choice of the appropriate plastic material. When cooled down, the plastic is reduced into the called for sizes or injury onto reels if the product is a plastic film or sheet - plastic extrusion. Comparing Plastic Extrusion to Other Plastic Forming Methods
Comprehending the kinds of plastic ideal for extrusion leads the way for a more comprehensive conversation on just how plastic extrusion piles up against other plastic developing methods. Couple of various other production procedures can match the speed of plastic extrusion.
Report this page